8 Leveraging Virtual Modelling For Digital Fabrication to Achieve Construction Efficiency
Simon Kigo Muhuga
Introduction
In the rapidly evolving landscape of construction, where time and resources are often in high demand, innovative solutions are continuously sought to streamline processes and enhance efficiency.
One such groundbreaking approach gaining traction is the integration of Virtual Modelling for Digital Fabrication technology (VMDF), a cutting-edge technology that merges digital design with advanced fabrication techniques.
Virtual Modelling for Digital Fabrication (VMDF) encompasses a design and production process where digital designs are modified within a virtual environment before being fabricated into physical objects.
In this workflow, designers utilize digital software such as SketchUp to model their designs, iterating and refining them virtually. This virtual iteration allows for thorough testing, validation, and optimization of designs.
The digital designs are then translated into physical form through fabrication techniques such as 3D printing, Computer Numerical Control (CNC) machining, or other manufacturing methods.
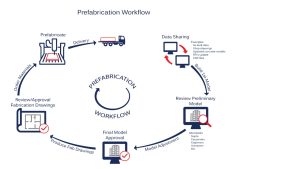
Rationale for studying the case
1. Motivation for the problem/research question
The motivation for studying the case of Virtual Modelling for Digital Fabrication (VMDF) in improving construction efficiency lies in the urgent need for transformative solutions within the construction industry.
Some traditional construction methods are often marred by inefficiencies, cost overruns, and delays, stemming from challenges such as design errors, material waste, and logistical complexities.
2. Purpose
By examining the integration of Virtual Modelling for Digital Fabrication (VMDF), we can uncover approaches to address some of these longstanding issues.
We can gain valuable insights into the potential benefits, challenges associated with the integration of Virtual Modelling for Digital Fabrication (VMDF), thereby paving the way for more efficient practices in the future.
3. Focus
This case study delves into the application of Virtual Modelling for Digital Fabrication (VMDF) within the context of the Seattle Aquarium Ocean Pavilion project, offering a compelling example of the technology’s transformative potential in improving construction efficiency.
We examine the implementation process of Virtual Modelling for Digital Fabrication (VMDF), highlighting the key stage of main tank and archipelago concrete walls construction.
We also discuss the challenges encountered, the solutions developed, and the tangible benefits realized through this innovative approach.
Detailed description of the facts related to the case
The Seattle Aquarium, a renowned marine conservation and education center, embarked on a significant expansion project to accommodate the growing visitor numbers and enhance its educational exhibits.
The Seattle Ocean Pavilion is two Storey 50,000 square feet [1] new building addition to Seattle’s iconic waterfront and aims to offer visitors a journey into the wonders of the ocean, showcasing diverse marine life and fostering conservation awareness for generations to come.
Situated along Alaskan Way, adjacent to the Seattle Aquarium on Pier 60, the project promises to redefine the city’s waterfront landscape.
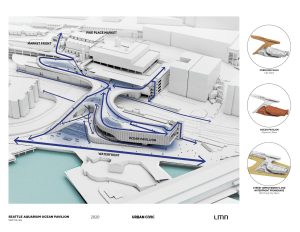
With a construction cost of $160 million [2] this project undertaking represents a significant investment in Seattle’s cultural and tourist infrastructure.
The project is set to be opened in Summer of 2024. Turner Construction is the general contractor for the project while LMN is the project architect [3].
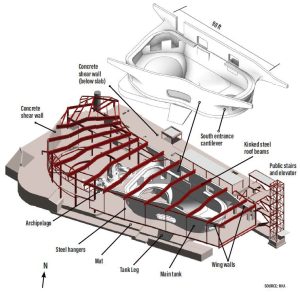
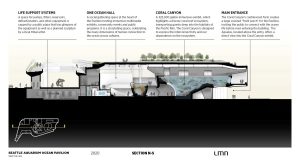
Faced with complex concrete formwork challenges characterized by the project’s unique architectural design with intricate and unconventional geometry, the general contractor turned to virtual modeling software to design custom formwork and overcome the complexities.
Traditional concrete formwork techniques would have been impractical and inefficient for constructing the tanks according to specifications.
By utilizing virtual modelling software, Turner’s Virtual Design Construction Engineers were able to visualize and break down the tank geometry, developing precise models and fabricating formwork solutions.
One of the areas Turner leveraged on virtual modelling was developing a concrete block out for the Coral Canyon also referred to as ‘Sharkilus’, a 20ft wide circular opening in the main tank.
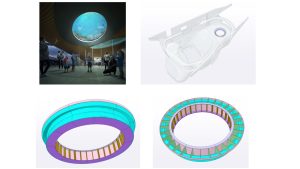
Fabrication drawings for the block out formwork components were produced then manufactured with unparalleled accuracy to accommodate the complex shape. CNC machining was the preferred advanced digital fabrication technique.
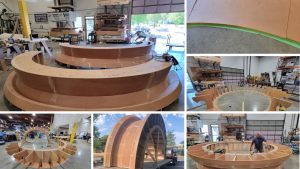
The acrylic glass notched into the opening once the concrete formwork had been removed.
The risk of errors, reworks and delays during the construction phase were mitigated by leveraging on Virtual Modelling for Digital Fabrication (VMDF).
This innovative had approach allowed for the seamless concrete pouring and curing of the tank’s walls.
Turner’s VDC Engineers also modelled formwork lift drawings for the foam inserts that were attached to metal formwork. These foam inserts created the intricate and complex curves of the main tank walls.
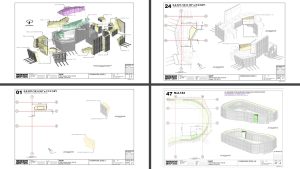
Turner collaborated with Janicki Industries to fabricate the foam inserts on a large scale. Each panel went through three companies before reaching the job site. The panels were CNC’ed foam glued to Peri backing and sprayed with a truck bed liner.

The project achieved remarkable efficiency gains, as time-consuming manual adjustments and rework were minimized, while resource utilization was optimized.
The seamless integration of Virtual Modelling and Digital Fabrication (VMDF) not only addressed concrete formwork problems but also showcased their broader applicability in streamlining construction processes and elevating project outcomes.
Description of the data collected
Overview
Interviews were conducted with two Virtual Design Construction (VDC) Managers at Turner Construction involved in the Seattle Aquarium Project.
The purpose of these interviews was to gain insights into their professional experiences, motivations, and perceptions related to the project, as well as to understand the specific contributions and impacts of Virtual Modification Digital Fabrication (VMDF) technology in the construction process.
1. Professional Background
The interviews began with general questions to establish the background and experience of the participants.
This included inquiries about how long the interviewees had been in the profession and the duration for which Turner Construction had maintained a Virtual Design Construction (VDC) Department.
These questions provided a foundational understanding of the participants’ expertise and the historical context of Virtual Design Construction (VDC) within the organization.
The initial questions aimed to gather basic professional background information:
- “How long have you been in the profession?”
- “How long has Turner Construction had a Virtual Design Construction (VDC) Department?”
2. Work-related Questions
The interviews progressed to explore work-related aspects, focusing on the motivations and roles of the VDC Managers in the context of Virtual Modification Digital Fabrication (VMDF) within the construction industry.
The questions aimed to uncover personal motivations and day-to-day responsibilities:
- “What motivated you to pursue a career in Virtual Modification Digital Fabrication (VMDF) within the construction industry?”
- “As a VDC Manager, what do you do?”
3. Experience and Perception of VMDF
Next, the interviews delved into the participants’ experience and perception of VMDF.
The questions aimed to understand how they define VMDF, identify key challenges and barriers to its adoption, and explore potential solutions.
Additionally, the interviews sought to highlight the benefits of implementing VMDF technologies:
- “How do you define Virtual Modification Digital Fabrication?”
- “What are some of the key challenges or barriers to the widespread adoption of VMDF in the construction sector?”
- “How can these challenges be addressed?”
- “What are the key benefits of implementing VMDF in construction?”
4. Project-Specific Questions
To obtain detailed insights related to the Seattle Aquarium project, the interviews included project-specific questions.
These questions focused on the role and impact of VMDF in the project, examining how it contributed to the accuracy of design and construction, prevented errors or rework, and enhanced efficiency.
The questions also explored any cost and time savings realized through the use of VMDF technologies:
- “Can you walk me through the role of Virtual Modification for Digital Fabrication (VMDF) in the Seattle Aquarium project?”
- “Can you discuss any cost and time savings realized as a result of implementing VMDF technology?”
5. Future of VMDF
Looking towards the future, the interviews also sought to understand the anticipated evolution of VMDF technology and their potential impact on the construction industry.
This forward-looking perspective aimed to gather thoughts on future advancements and the broader implications for the industry:
- “How do you anticipate VMDF technologies evolving in the near future and what impact do you think these advancements will have on the construction industry?”
6. Conclusion
To conclude the interviews, participants were asked if they had any questions for the interviewer.
The structured approach of the interviews ensured comprehensive data collection, covering professional experiences, specific project details, and future outlooks.
This information is critical for understanding the role of VMDF in the Seattle Aquarium Project and its broader implications in the construction industry.
Data Analysis
The data collected from the interviews was systematically analyzed to uncover patterns, themes, and insights relevant to the Seattle Aquarium Ocean Pavilion Project.
Each interview was transcribed and then coded to identify key themes and categories that emerged from the responses.
This coding process allowed for the organization and synthesis of qualitative data, facilitating a comprehensive analysis of the participants’ experiences, perceptions, and the specific impacts of Virtual Modification Digital Fabrication (VMDF) technology on the project.
By structuring the data in this manner, we were able to draw meaningful conclusions and make informed recommendations based on the rich insights provided by the interviewees.
Discussion of the patterns/theories found
1. Professional Background and Experience
Both interviewees have extensive experience between 10-13 years in the profession.
Turner Construction’s VDC department has been established for approximately 16-17 years, providing a solid foundation for VMDF practices.
The extensive experience of both interviewees in architecture and digital fabrication underscores the value of transitioning from design to practical application in construction.
Their careers highlight the growing importance of VMDF in modern construction practices.
2. Motivations for Pursuing VMDF
Both interviewees were motivated by their backgrounds in architecture and early exposure to digital fabrication.
They recognized the potential to advance models from conceptual designs to practical construction applications.
Roles and Responsibilities
As VDC Managers, both interviewees focus on managing workflows, budgets, and teams.
They are also involved in creating accurate and detailed models, coordinating with various departments.
Their roles also include training staff and overseeing the use of fabrication machines.
Definitions and Perceptions of VMDF
VMDF is seen as a two-step process of creating detailed digital models that serve as accurate representations of what will be built on-site and
then defining instructions that machines use to fabricate parts.
This process, effectively creating a digital twin, ensures precision.
Challenges in Adopting VMDF
Major challenges include lack of exposure and familiarity, high capital costs, and managing large amounts of data.
There is also a need for accurate information at the right time and place, making the process complex and lengthy.
Solutions to Challenges
Both interviewees advocate for a phased approach by starting small and testing with smaller machines before scaling up which can help build confidence in VMDF.
Demonstrating successful implementations and optimizing investments gradually are key strategies to overcome resistance and justify larger expenditures.
Benefits of Implementing VMDF
The primary benefits include significant cost and time savings, reduced on-site errors, and better planning and coordination.
Detailed pre-construction modeling allows for issues to be resolved in the virtual environment, leading to more efficient construction processes.
Project-Specific Insights
In the Seattle Aquarium project, VMDF was crucial for creating complex concrete forms and ensuring precise construction.
The use of detailed models facilitated collaboration among stakeholders from different disciplines and prevented errors and rework, particularly in the main tank’s complex geometry.
Cost and Time Savings
Implementing VMDF resulted in substantial labor and time savings.
Cost savings were in terms of labor expenditure reduction in terms of the man hours taken to manufacture the formwork, man hours taken to conduct formwork adjustments on site and elimination of man hours for conducting rework versus the traditional method that have to account for these man hours.
Accurate models reduced the time required for repetitive tasks and minimized errors, leading to cost-effective and efficient construction processes.
Future of VMDF
The future of VMDF appears promising VMDF technology is expected to continue evolving with advancements in automation, robotics, and digital modeling techniques.
The integration of coding and scripting will further automate tasks, making construction processes faster and more accurate.
The scope of VMDF applications is also expanding beyond specific formwork to other building parts and job site items, indicating a broader impact on the construction industry.
Theory found
Continuous evolution and integration of advanced VMDF technologies, such as automation, robotics, and coding, will significantly transform the construction industry by improving efficiency, accuracy, and cost-effectiveness.
Connection to the larger scheme of things
-
Technological Advancement in Construction
The case study exemplifies the ongoing technological advancement in the construction industry, particularly in the realm of digital technologies.By showcasing the application of Virtual Modification Digital Fabrication (VMDF), the study highlights how innovative tools and methodologies are reshaping traditional construction practices and driving efficiency and precision in building projects.
-
Sustainable Construction Practices
Within the context of sustainable development, the case study underscores the importance of adopting environmentally friendly construction practices. Virtual Modification Digital Fabrication (VMDF) techniques offer the potential to minimize material wastage, optimize resource utilization, and reduce carbon footprint, aligning with global efforts to promote sustainable construction methods and mitigate environmental impact.
-
Knowledge Sharing and Collaboration
Through the dissemination of findings and insights from the case study, the research contributes to knowledge sharing and collaboration within the construction industry. By sharing best practices, lessons learned, and recommendations, the study facilitates cross-disciplinary dialogue, fosters collaboration among stakeholders, and promotes the adoption of innovative technologies and methodologies.
-
Economic and Social Impacts
The implementation of Virtual Modification Digital Fabrication (VMDF), techniques in construction projects can have significant economic and social impacts at both local and global levels. By improving construction efficiency, reducing project timelines, and enhancing quality and safety standards, virtual modification technologies contribute to economic growth, job creation, and infrastructure development, benefiting communities and society at large.
-
Future Directions and Opportunities
Finally, the case study serves as a catalyst for future research, innovation, and investment in construction technology and sustainability. By identifying emerging trends, challenges, and opportunities, the study informs strategic decision-making and resource allocation, guiding industry stakeholders toward a more resilient, efficient, and sustainable built environment.
References
[1] N. M. Post, “Seattle’s Audacious Aquarium Throws Builders Swerves, Curves, Twists and Turns,” 20 December 2023. [Online]. Available: https://www.enr.com/articles/57902-seattles-audacious-aquarium-throws-builders-swerves-curves-twists-and-turns. [Accessed 16 May 2024].
[2] Seattle Aquarium, “Ocean Pavilion Progress,” n.d. [Online]. Available: https://www.seattleaquarium.org/explore-the-aquarium/campus/ocean-pavilion/progress/. [Accessed 16 05 2024].
[3] LMN Architects, “Seattle Aquarium Ocean Pavillion,” LMN Architects, n.d. [Online]. Available: https://lmnarchitects.com/project/seattle-aquarium-ocean-pavilion. [Accessed 20 April 2024].
Media Attributions
- Prefabrication Workflow © Turner Construction
- Seattle-Aquarium-Ocean-Pavilion_Project Location © LMN Architects
- MKA Seattle Acquarium © Nadine M. Post
- Seattle-Aquarium-Ocean-Pavilion_B-2000×1545 © LMN Architects
- Seattle-Aquarium-Ocean-Pavilion_Sharkillus Blockout © Turner Construction
- Seattle-Aquarium-Ocean-Pavilion_Sharkillus Blockout CNC © Turner Construction
- Formwork lift drawings © Turner Construction
- Turner’s ^M Janicki © Turner Construction